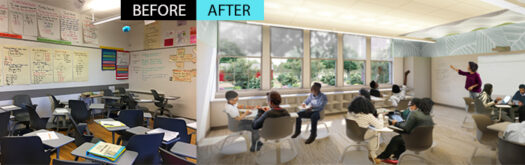
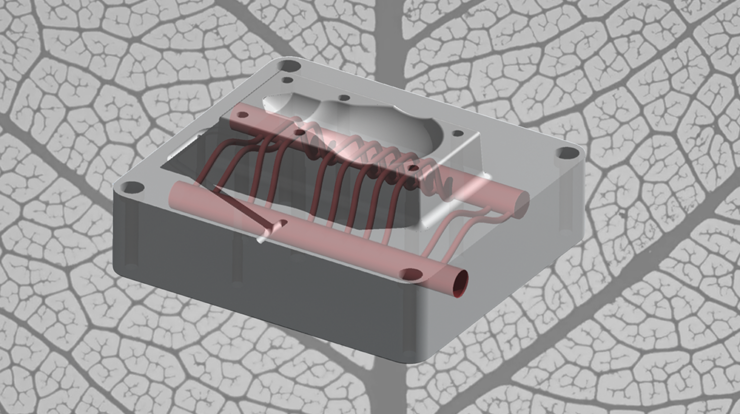
Features
New Bioinspired Innovation Case Study: Efficient Heat Transfer in Manufacturing
Cas Smith
Share
Learn more about our bioinspired innovation work and services by emailing us at [email protected] and reading our report, Tapping into Nature. Follow the conversation on twitter: @TerrapinBG | #TapNature.
We’re excited to announce that we have released the first in a series of bioinspired innovation case studies exploring Terrapin’s work helping companies overcome technology challenges. This case study builds on our report Tapping into Nature, which explores examples of bioinspired technologies and the opportunities of a biologically-inspired approach to innovation. This first entry details how Terrapin assisted HARBEC Inc., a plastic and metal parts manufacturer, in utilizing bioinspired design to improve a key manufacturing process.
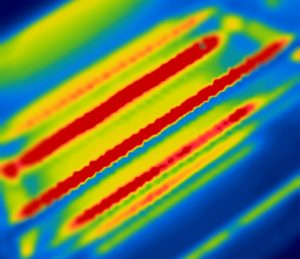
A false color image captured using an infrared camera reveals the heat emitted during a manufacturing process. Red areas denote higher temperatures.
Image © Cas Smith
Like all injection molding processes, HARBEC heats solid plastic until it liquefies, presses the molten plastic into the cavity of a mold, and waits for the part to cool before ejecting it. This series of steps—melt, press, cool, eject—is called a cycle. When thousands or even millions of parts are being manufactured for a customer, the duration of each cycle is critical, and HARBEC knew that the cooling step was adding up to significant time and energy costs.
The project focused on the challenge of decreasing the time and energy spent during the cooling phase of the injection molding process. Turning to the many cooling systems in nature for inspiration, Terrapin worked with HARBEC’s engineering and manufacturing teams as well as topical experts from our network to innovate on current designs. After abstracting the underlying principles of the fluid-carrying channels in certain leaves, the project team combined these insights with the capabilities of additive manufacturing. The result is a design that reduces the time and energy used by more than 20% compared to conventional solutions. Read the case study for the full account of how we unlocked these significant energy and time savings!
View and download the case study pdf below:
Efficient Heat Transfer in Manufacturing – HARBEC – PDF (1.8 MB)
Looking for more solutions to technology challenges? Check out our report on how bioinspired innovation can solve technology challenges in nine wide-ranging areas related to manufacturing and industry!
*Feature images copyright Jon Connell/Flickr, smshubert6/Flickr, and Andrew Magill/Flickr. Header image copyright HARBEC & Terrapin Bright Green.
Filed under:
Cas Smith
Cas is a biological engineer with a passion for technology based in and inspired by biology. He served as the project manager for Terrapin's technology development services. Cas believes that using biotechnology will lead to a more bountiful and prosperous world for all living things.
Topics
- Environmental Values
- Speaking
- LEED
- Terrapin Team
- Phoebe
- Community Development
- Greenbuild
- Technology
- Biophilic Design Interactive
- Catie Ryan
- Spanish
- Hebrew
- French
- Portuguese
- Publications
- Occupant Comfort
- Materials Science
- Conference
- Psychoacoustics
- Education
- Workshop
- Mass Timber
- Transit
- Carbon Strategy
- connection with natural materials
- interior design
- inspirational hero
- biophilia
- economics of biophilia
- Sustainability
- wood
- case studies
- Systems Integration
- Biophilic Design
- Commercial
- Net Zero
- Resorts & Hospitality
- Energy Utilization
- Water Management
- Corporations and Institutions
- Institutional
- Ecosystem Science
- Green Guidelines
- Profitability
- Climate Resiliency
- Health & Wellbeing
- Indoor Environmental Quality
- Building Performance
- Bioinspired Innovation
- Biodiversity
- Residential
- Master Planning
- Architects and Designers
- Developers and Building Owners
- Governments and NGOs
- Urban Design
- Product Development
- Original Research
- Manufacturing
- Industrial Ecology
- Resource Management
- Sustainability Plans
- Health Care
- Carbon Neutrality